A5tr0 An0n
Well-Known Member
- Joined
- Sep 29, 2012
- Messages
- 521
- Reaction score
- 10
Intro:
ac·qui·si·tion: 2. the learning or developing of a skill, habit, or quality.
Since the grounding of my L3 flight due to weather, I have since scratched that vehicle and redesigned the L3. So I noticed that I had some 38mm and 54mm motors in the closet and thought why not scale the design down and burn some. I have helped build two other fin can on motor case designs and have been wanting to acquire more information on them, hence the name. Short of attaching the fins directly to the case, I am looking to see if this is a more efficient design vs a traditional MD design, and if in fact it is, by how much? My assumption says yes but empirical flight data seems like the quickest and easiest method of finding out. I see pros and cons to both methods and before starting to build the bird for the L3, I wish to acquire more information/experience with flying cases. I am also taking this as a chance to prefect the simulation tools. I have noticed that there are more than one ways to design a flying case and all of the ways produce different results, so I can use this to find the best method.
So here is how it is going to go - more or less. I will build a "flying case," and a conventional MD version of the same vehicle. The plan is for them to be identical to one another (except the obvious), and to fly on the same motor. I am starting with the flying case which this thread will cover and will address the conventional MD in a later thread (likewise with the 54s) .
Design:
The design thoughts are to reduce the minimum diameter by a little as compared to a conferential minimum diameter so perhaps a absolute minimum diameter is more appropriate. Furthermore the thoughts were to reduce materials and therefore overall mass, to do so the motor case is being used as the airframe. Thicknesses are down to lowest level I am comfortable with, including nose cone, upper airframe, fin can, couplers, and fins. Finally to build on the previous work of myself and others in the flying case arena. More technical details below.
Technical Specifications:
**All laminated parts were done so with Proline 4100 Epoxy and structurally epoxied parts used Proline 4500.**
Nose Cone: 6:1 Ogive FWFG Nose Cone measuring 9" Length (6:1 duh), 1.5" Max OD, 1.42" Max ID, 0.04" Wall Thickness, and 0.075lb Mass. No permanently fixed coupler.
Payload: This is the electrical payload bay and also the NC/AF coupler. Hand laid fiberglass (S2) 301.76gsm 8 Harness Satin Weave measuring 6" Length, 1.379" OD, 1.225" ID, 0.077" Wall Thickness, and 0.129lb Mass. The Payload section will be shear pinned to the nose cone and bolted to the UAF/Motor Case Coupler.
Upper Airframe: Seeing as there is no airframe over the motor due to the motor being the airframe, I am calling the tube that couples to the top of the motor the "upper airframe." Hand laid Carbon Fiber 3k 7.5oz measuring 6.09" Length, 1.5" OD, 1.42" ID, 0.04" Wall Thickness, and 0.071lb. Payload tube utilizes standard bulkheads each 0.09" Thick x4 bulkheads, summing 0.032lb Mass.
Motor Adapter / Coupler: Motor Adapter is the Aeropack Delay/Eject-Closure Adapter (motor is plugged); this allows me to attach a bolt to the motor's forward closure, this will be used to secure the motor to the upper airframe. The coupler will rest over the adapter and on the motor case; the upper airframe slides over this and is countersunk into the coupler for security. Through the use of the adapter the closure is bolted into the top of the motor. The Coupler is hand laid Carbon Fiber 12k 19.9oz measuring 1.5" Length, 1.42" OD, 0.5" ID, 0.46" Wall Thickness, and 0.2lb Mass.
Lower Airframe / Motor Case: The lower airframe IS the motor case and is made from anodized 6061 Aluminum, I believe (?) and measures 19.71" Length, 1.5" OD, X" ID, X" Wall Thickness, and Xlb Mass (Loaded Mass = 2.10lb, Burnout Mass = 0.78lb).
Fin Can Transition/Shoulder: The fin can shoulder is a transitional part that transitions the motor case/airframe to the fin can. This should provide a more aerodynamic flow and should prevent a majority of the flow from going underneath the fin can. The should is a hand laid Carbon Fiber 3k 7.5oz that is actually a single part with the fin can, I have just separated the two parts for description purposes. The fin can shoulder is more or less conceal in shape and measures 0.75" Length, 1.5" Fore Diameter, 1.58" Aft Diameter, 0.04" Wall Thickness, and 0.009lb Mass.
Fin Can: The fin can slides over the motor casing until it reaches the motor aft closure, which prevents it from moving aft. The fin can will be friction fit into place, hopefully preventing any rotation of the fin can during flight. The fin can is made from hand laid Carbon Fiber 3k 7.5oz measuring 7" Length, 1.58" OD, 1.5" ID, 0.04" Wall Thickness, and 0.087lb Mass.
Fins: This vehicle utilizes a 3 fin design as opposed to a 4 fin design. The reasons for this is greater dynamic stability is not needed, the tower is designed for 3 fins, easier work, less materials, and possibly less drag. To negate the aforementioned I would need to make the 4 fins smaller, which is not really possible given the span as of now is already very small. The fins are a standard swept back clipped delta; this is my first time incorporating a swept back design. I have been reluctant to use swept back fins in the past for structural concerns, a lesser portion of the fin is supported. However after looking at other successful flights I feel quite confident in the design. The move for swept back fins was for the increase in performance that they are forecasted to bring, however at a trade off in slight overall stability. The fins are made from Quasi-isotropic Twill/Uni blend Carbon Fiber (yes they alternate by 0/90 degrees) and measure 6" Root Chord, 0.5" Tip Chord, 1.35" Span, 5.75" Sweep Length, 76.8 degree Sweep Angle, 0.043lb Mass, and 0.06" Thickness. The fins are located 28.05" from the tip of the nose cone.
Deployment / Recovery: Deployment will be via a cable cutter wrapped around the main parachute (only parachute) that is housed in the nose cone. At apogee the nose cone separates from the coupler/airframe via a Xg BP charge, pulling the wrapped parachute out into the atmosphere. At the designated main altitude (1500ft) the cable wrapping the parachute is sheared and the main unfolds and inflates slowing the vehicle down. Recovery Parachute size TBD.
Electronics: The flight computers will consist of a SL100 x1, and either a AIM XTRA x1 OR a TeleMega x1. The GPS tracking will consist of either AIM XTRA x1 OR a TeleMega x1. All electronics will be housed in the payload section.
Launch Method: This vehicle will be tower launched, meaning no rail buttons, struts, etc. The tower is a adjustable tower that I built previously and was designed for 3 finned vehicles (one of the reason this vehicle is 3 fins). If you would like more information, you can find it here -> https://www.rocketryforum.com/showthread.php?67902-Versatility-Adjustable-Launch-Tower.
Conclusion:
This will be a work in progress coming soon.
Disclaimer:
If you have any thoughts or any papers to read on the subjects mentioned above please feel free to share. Also if you spot any mistakes in the above text or any to follow please let me know so I can edit it appropriately.
I will be added the actual metrics once I finish making the parts, so keep in mind the above listed is just the planned dimensions and they will more likely than not change.
ac·qui·si·tion: 2. the learning or developing of a skill, habit, or quality.
Since the grounding of my L3 flight due to weather, I have since scratched that vehicle and redesigned the L3. So I noticed that I had some 38mm and 54mm motors in the closet and thought why not scale the design down and burn some. I have helped build two other fin can on motor case designs and have been wanting to acquire more information on them, hence the name. Short of attaching the fins directly to the case, I am looking to see if this is a more efficient design vs a traditional MD design, and if in fact it is, by how much? My assumption says yes but empirical flight data seems like the quickest and easiest method of finding out. I see pros and cons to both methods and before starting to build the bird for the L3, I wish to acquire more information/experience with flying cases. I am also taking this as a chance to prefect the simulation tools. I have noticed that there are more than one ways to design a flying case and all of the ways produce different results, so I can use this to find the best method.
So here is how it is going to go - more or less. I will build a "flying case," and a conventional MD version of the same vehicle. The plan is for them to be identical to one another (except the obvious), and to fly on the same motor. I am starting with the flying case which this thread will cover and will address the conventional MD in a later thread (likewise with the 54s) .
Design:
The design thoughts are to reduce the minimum diameter by a little as compared to a conferential minimum diameter so perhaps a absolute minimum diameter is more appropriate. Furthermore the thoughts were to reduce materials and therefore overall mass, to do so the motor case is being used as the airframe. Thicknesses are down to lowest level I am comfortable with, including nose cone, upper airframe, fin can, couplers, and fins. Finally to build on the previous work of myself and others in the flying case arena. More technical details below.
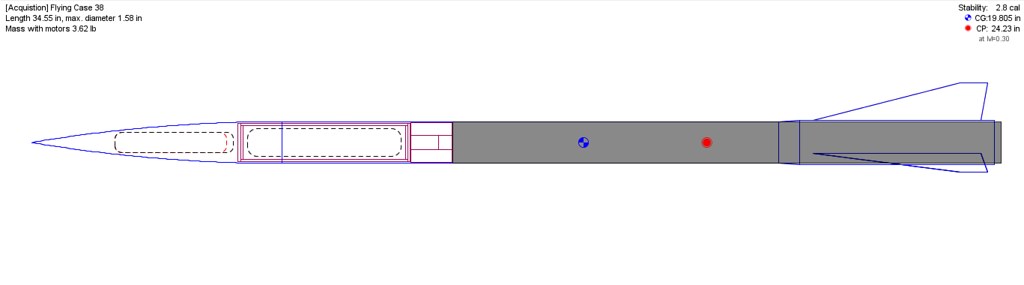
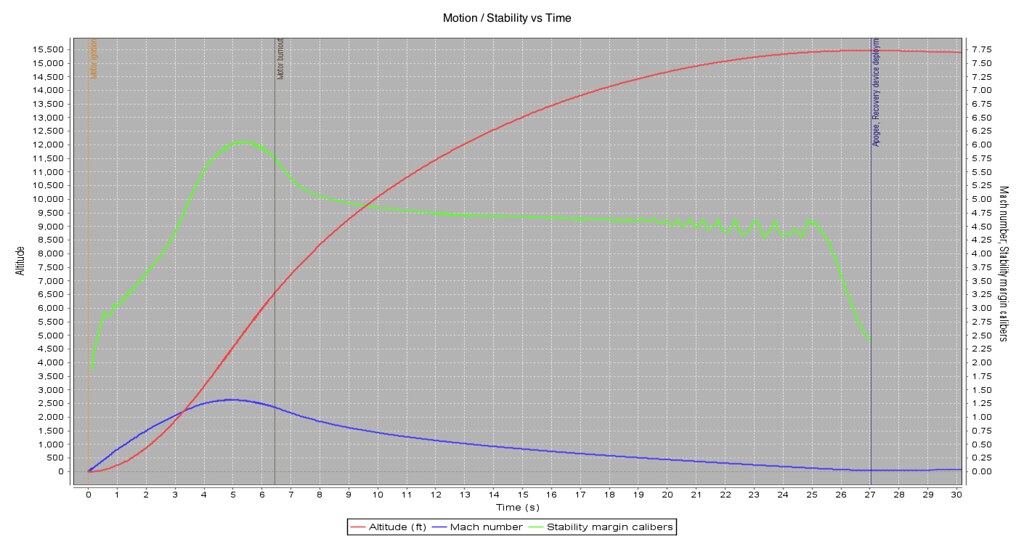
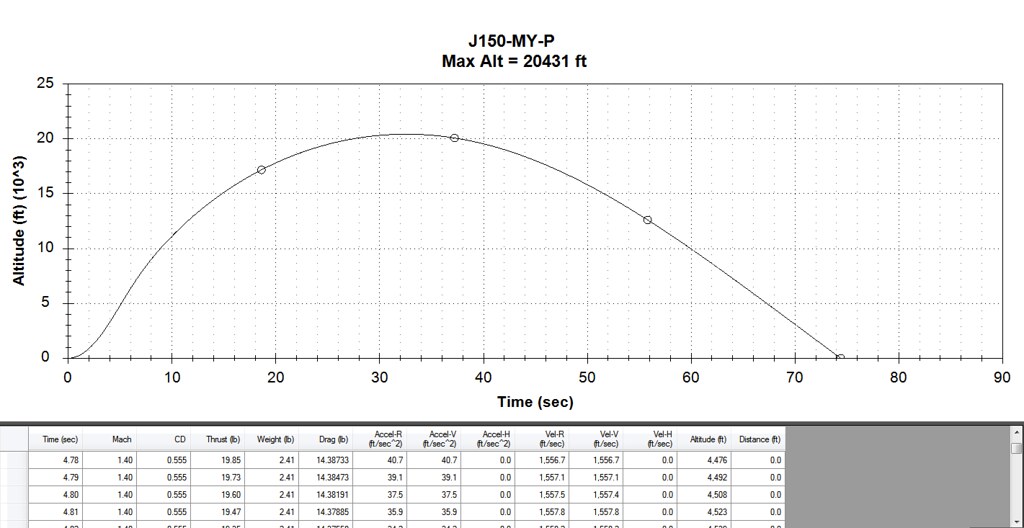
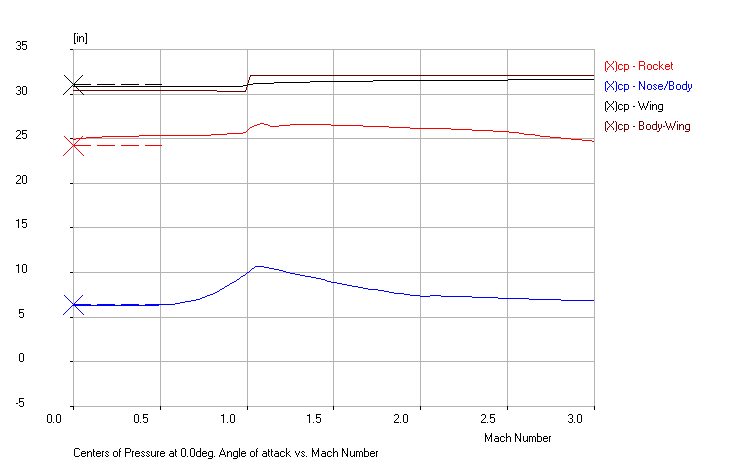
Technical Specifications:
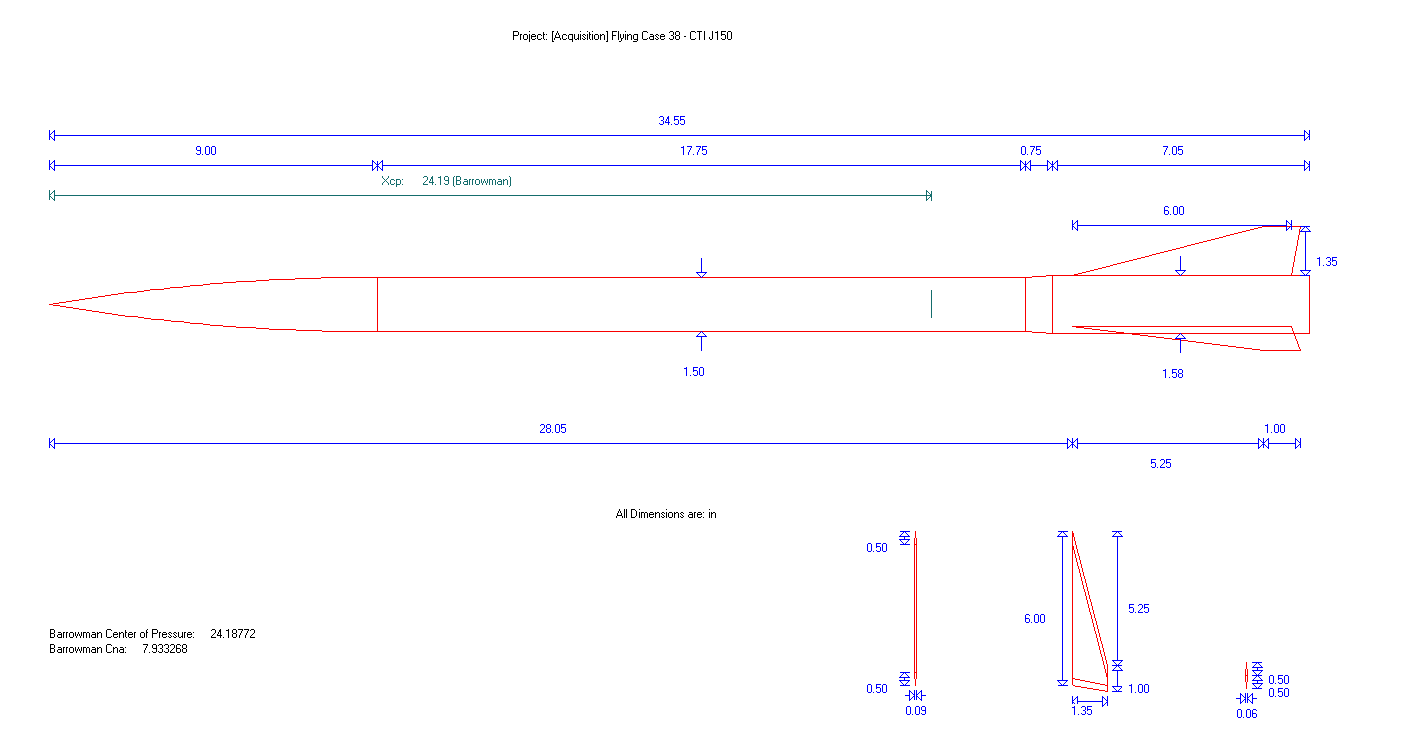
**All laminated parts were done so with Proline 4100 Epoxy and structurally epoxied parts used Proline 4500.**
Nose Cone: 6:1 Ogive FWFG Nose Cone measuring 9" Length (6:1 duh), 1.5" Max OD, 1.42" Max ID, 0.04" Wall Thickness, and 0.075lb Mass. No permanently fixed coupler.
Payload: This is the electrical payload bay and also the NC/AF coupler. Hand laid fiberglass (S2) 301.76gsm 8 Harness Satin Weave measuring 6" Length, 1.379" OD, 1.225" ID, 0.077" Wall Thickness, and 0.129lb Mass. The Payload section will be shear pinned to the nose cone and bolted to the UAF/Motor Case Coupler.
Upper Airframe: Seeing as there is no airframe over the motor due to the motor being the airframe, I am calling the tube that couples to the top of the motor the "upper airframe." Hand laid Carbon Fiber 3k 7.5oz measuring 6.09" Length, 1.5" OD, 1.42" ID, 0.04" Wall Thickness, and 0.071lb. Payload tube utilizes standard bulkheads each 0.09" Thick x4 bulkheads, summing 0.032lb Mass.
Motor Adapter / Coupler: Motor Adapter is the Aeropack Delay/Eject-Closure Adapter (motor is plugged); this allows me to attach a bolt to the motor's forward closure, this will be used to secure the motor to the upper airframe. The coupler will rest over the adapter and on the motor case; the upper airframe slides over this and is countersunk into the coupler for security. Through the use of the adapter the closure is bolted into the top of the motor. The Coupler is hand laid Carbon Fiber 12k 19.9oz measuring 1.5" Length, 1.42" OD, 0.5" ID, 0.46" Wall Thickness, and 0.2lb Mass.
Lower Airframe / Motor Case: The lower airframe IS the motor case and is made from anodized 6061 Aluminum, I believe (?) and measures 19.71" Length, 1.5" OD, X" ID, X" Wall Thickness, and Xlb Mass (Loaded Mass = 2.10lb, Burnout Mass = 0.78lb).
Fin Can Transition/Shoulder: The fin can shoulder is a transitional part that transitions the motor case/airframe to the fin can. This should provide a more aerodynamic flow and should prevent a majority of the flow from going underneath the fin can. The should is a hand laid Carbon Fiber 3k 7.5oz that is actually a single part with the fin can, I have just separated the two parts for description purposes. The fin can shoulder is more or less conceal in shape and measures 0.75" Length, 1.5" Fore Diameter, 1.58" Aft Diameter, 0.04" Wall Thickness, and 0.009lb Mass.
Fin Can: The fin can slides over the motor casing until it reaches the motor aft closure, which prevents it from moving aft. The fin can will be friction fit into place, hopefully preventing any rotation of the fin can during flight. The fin can is made from hand laid Carbon Fiber 3k 7.5oz measuring 7" Length, 1.58" OD, 1.5" ID, 0.04" Wall Thickness, and 0.087lb Mass.
Fins: This vehicle utilizes a 3 fin design as opposed to a 4 fin design. The reasons for this is greater dynamic stability is not needed, the tower is designed for 3 fins, easier work, less materials, and possibly less drag. To negate the aforementioned I would need to make the 4 fins smaller, which is not really possible given the span as of now is already very small. The fins are a standard swept back clipped delta; this is my first time incorporating a swept back design. I have been reluctant to use swept back fins in the past for structural concerns, a lesser portion of the fin is supported. However after looking at other successful flights I feel quite confident in the design. The move for swept back fins was for the increase in performance that they are forecasted to bring, however at a trade off in slight overall stability. The fins are made from Quasi-isotropic Twill/Uni blend Carbon Fiber (yes they alternate by 0/90 degrees) and measure 6" Root Chord, 0.5" Tip Chord, 1.35" Span, 5.75" Sweep Length, 76.8 degree Sweep Angle, 0.043lb Mass, and 0.06" Thickness. The fins are located 28.05" from the tip of the nose cone.
Deployment / Recovery: Deployment will be via a cable cutter wrapped around the main parachute (only parachute) that is housed in the nose cone. At apogee the nose cone separates from the coupler/airframe via a Xg BP charge, pulling the wrapped parachute out into the atmosphere. At the designated main altitude (1500ft) the cable wrapping the parachute is sheared and the main unfolds and inflates slowing the vehicle down. Recovery Parachute size TBD.
Electronics: The flight computers will consist of a SL100 x1, and either a AIM XTRA x1 OR a TeleMega x1. The GPS tracking will consist of either AIM XTRA x1 OR a TeleMega x1. All electronics will be housed in the payload section.
Launch Method: This vehicle will be tower launched, meaning no rail buttons, struts, etc. The tower is a adjustable tower that I built previously and was designed for 3 finned vehicles (one of the reason this vehicle is 3 fins). If you would like more information, you can find it here -> https://www.rocketryforum.com/showthread.php?67902-Versatility-Adjustable-Launch-Tower.
Conclusion:
This will be a work in progress coming soon.
Disclaimer:
If you have any thoughts or any papers to read on the subjects mentioned above please feel free to share. Also if you spot any mistakes in the above text or any to follow please let me know so I can edit it appropriately.
I will be added the actual metrics once I finish making the parts, so keep in mind the above listed is just the planned dimensions and they will more likely than not change.