Cory
Well-Known Member
I have spent tons of time trolling build threads, and finally decided to try one for myself. I will be building a MC ARCAS, planning on DD using a Stratologger for deployment control and BRB 900 for tracking. I decided to start with the e-bay.
I am using a LOC e-bay, I first cut the mounting tubes and sled. I have also fitted the e-bay with welded eye bolts purchased from Aeropack, Nylock nuts, and will be using the rotary switch pictured.
2.56" does not leave much room inside an e-bay, so after reading several threads concerning LiPo batteries, I am trying one for my first time.
I started by measuring, drilling, and tapping the 4-40 mounts for the Stratologger, then drilled and mounted the switch.
I'm using a technique found right here on TRF to help guide the screwdriver to the rotary switch by using half a wire nut.
I made a cutout in foam to fit the LiPo, and then cut a cover out of the same foam. I drilled four holes and zip-tied directly to the sled.
Now to epoxy the sled and any loose ends.
Next is the e-bay bulkheads.
I am using a LOC e-bay, I first cut the mounting tubes and sled. I have also fitted the e-bay with welded eye bolts purchased from Aeropack, Nylock nuts, and will be using the rotary switch pictured.
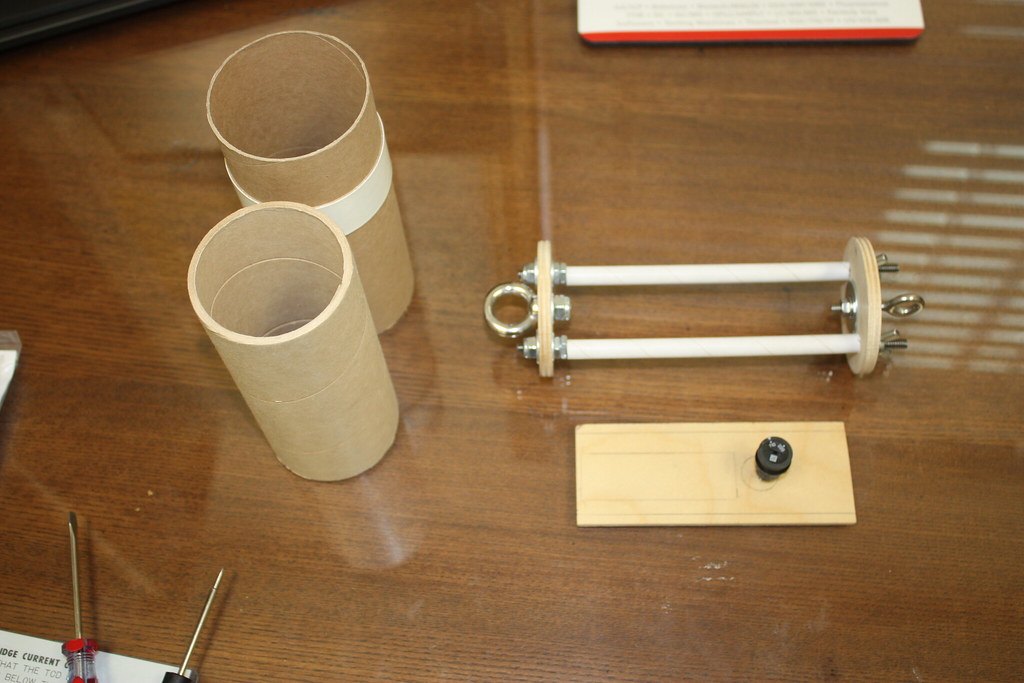
2.56" does not leave much room inside an e-bay, so after reading several threads concerning LiPo batteries, I am trying one for my first time.
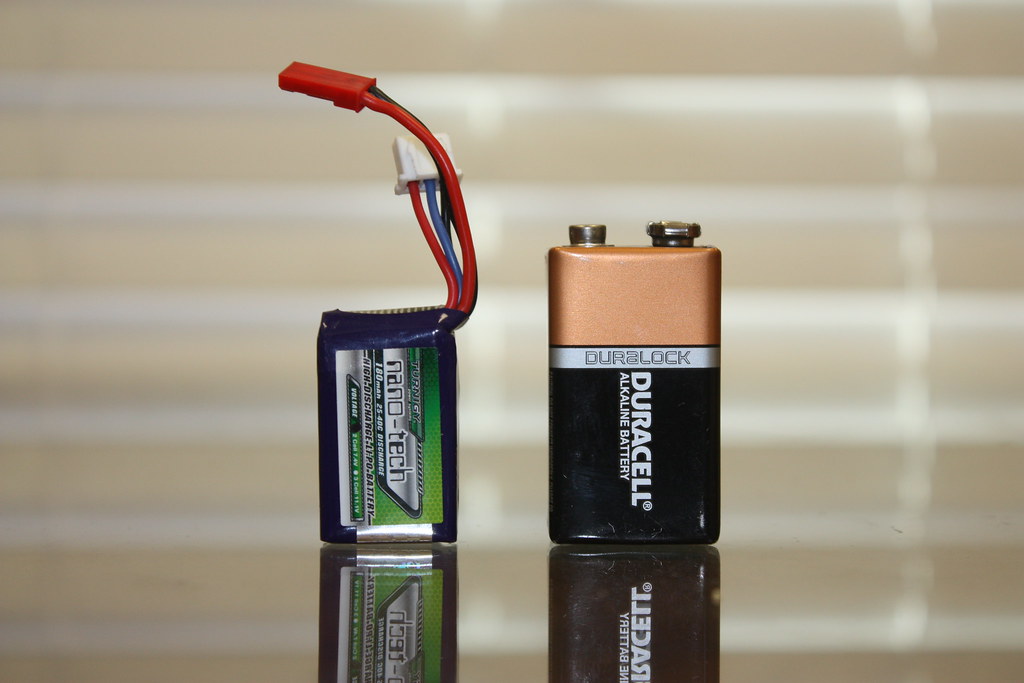
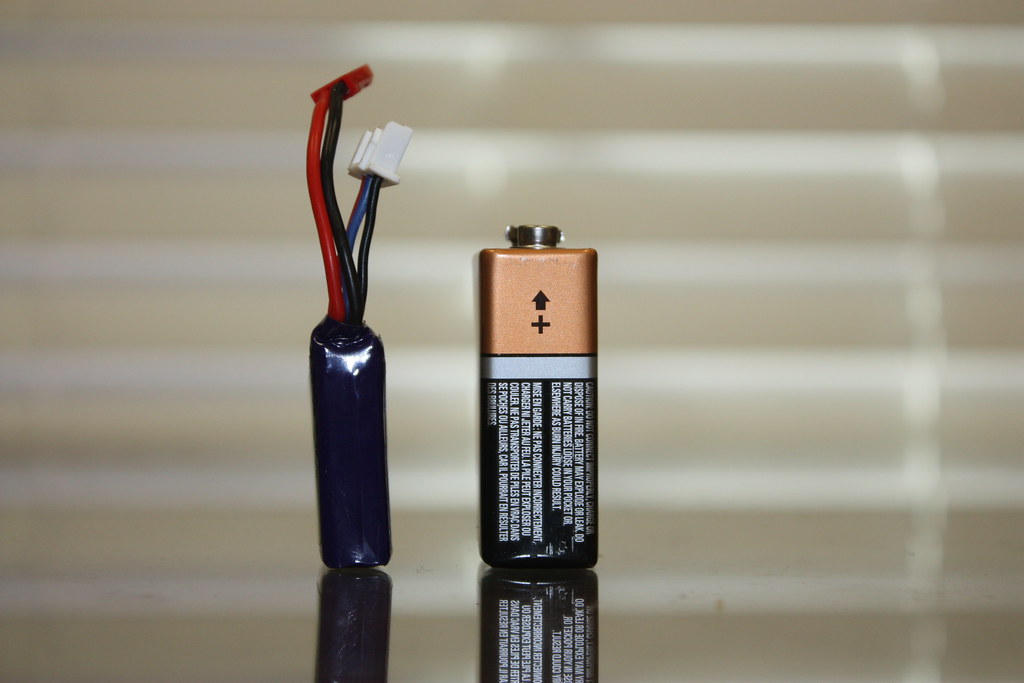
I started by measuring, drilling, and tapping the 4-40 mounts for the Stratologger, then drilled and mounted the switch.
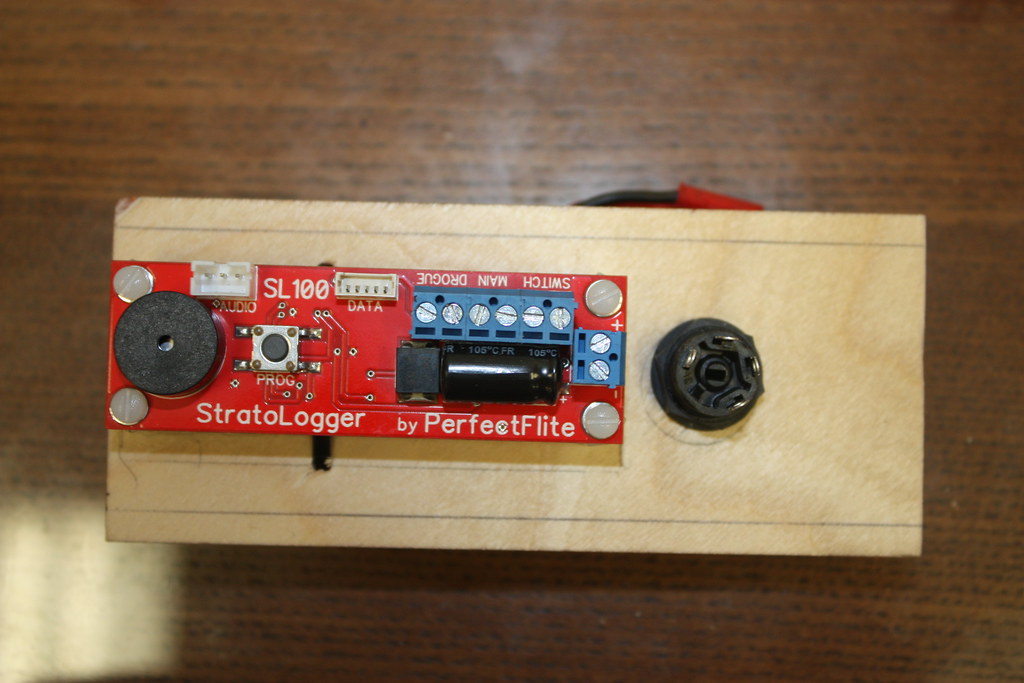
I'm using a technique found right here on TRF to help guide the screwdriver to the rotary switch by using half a wire nut.
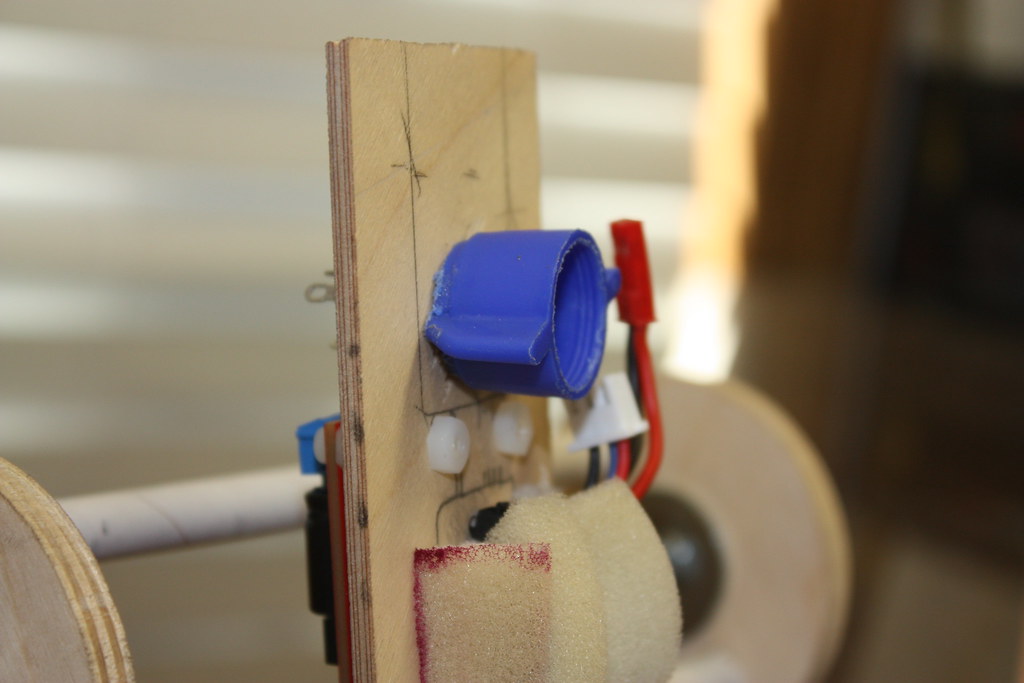
I made a cutout in foam to fit the LiPo, and then cut a cover out of the same foam. I drilled four holes and zip-tied directly to the sled.
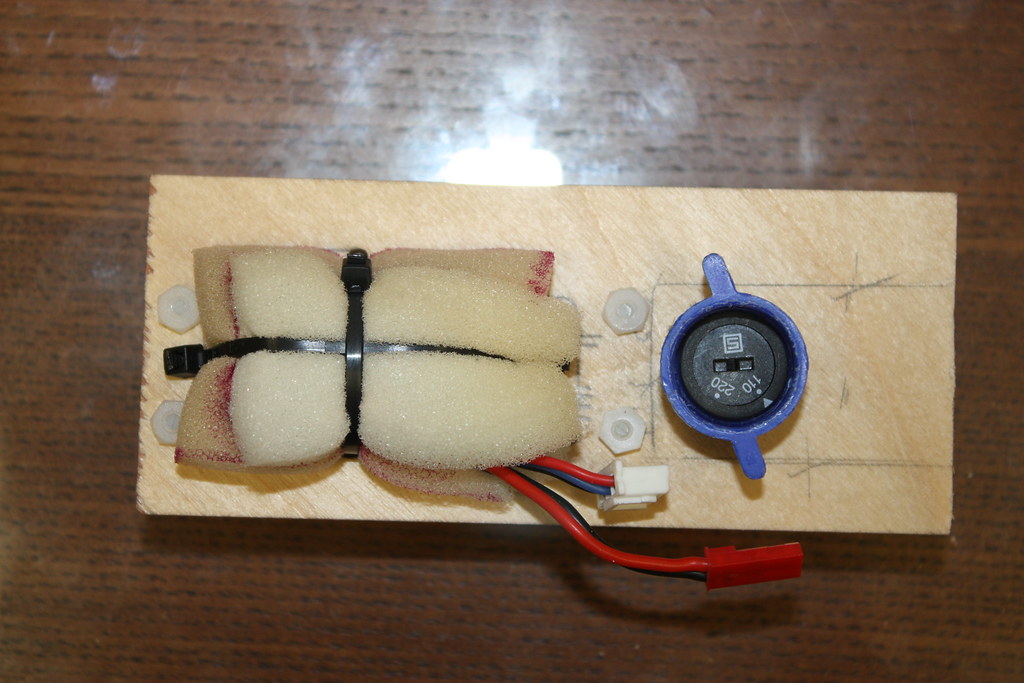
Now to epoxy the sled and any loose ends.
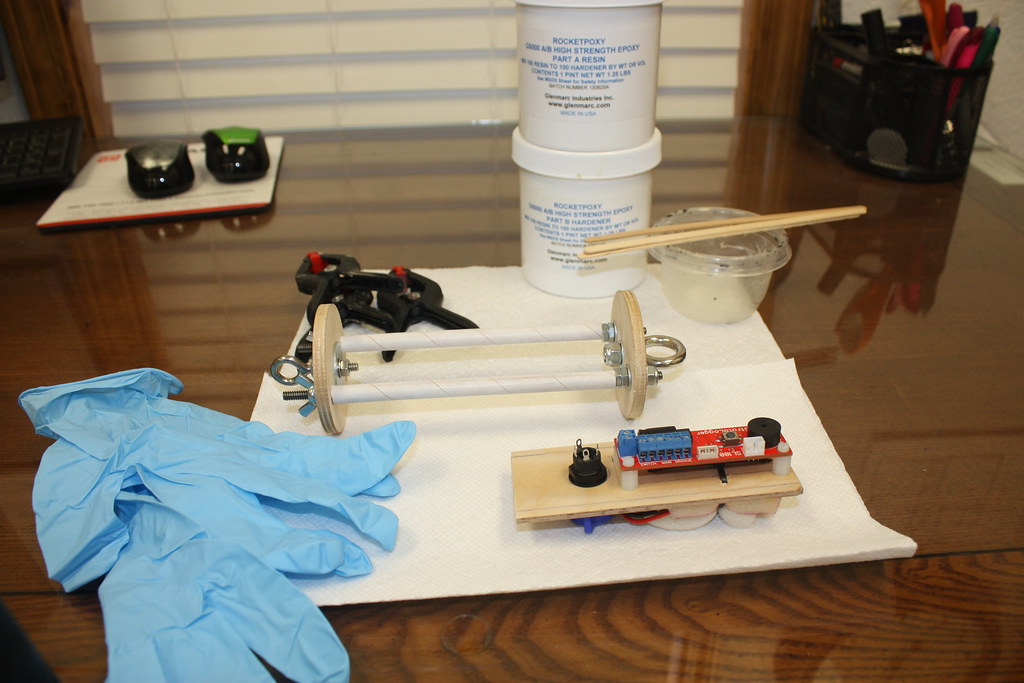
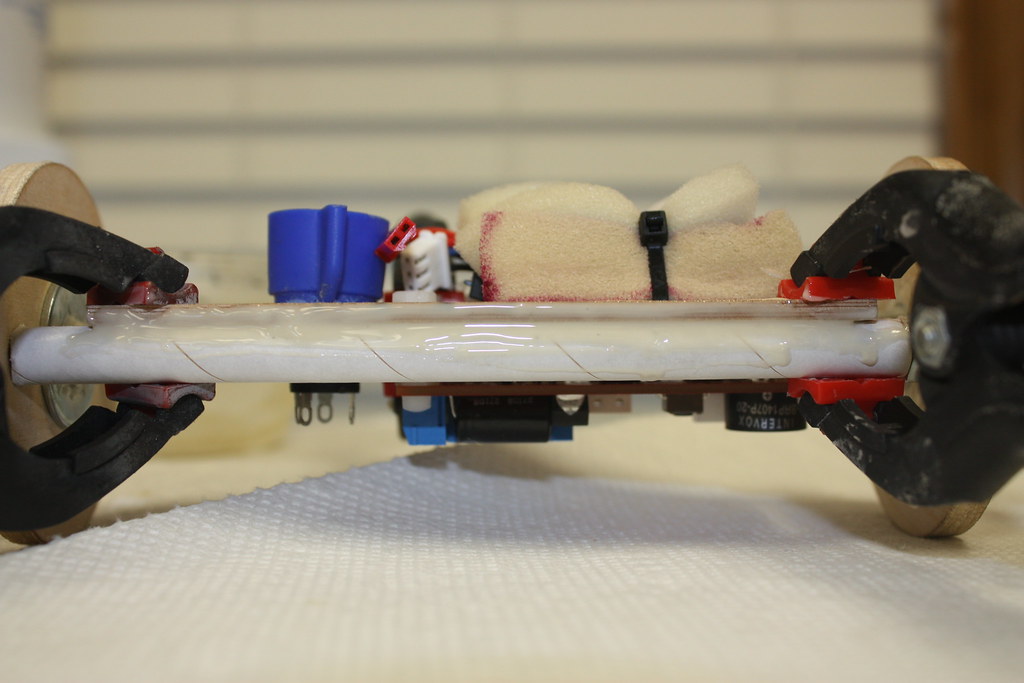
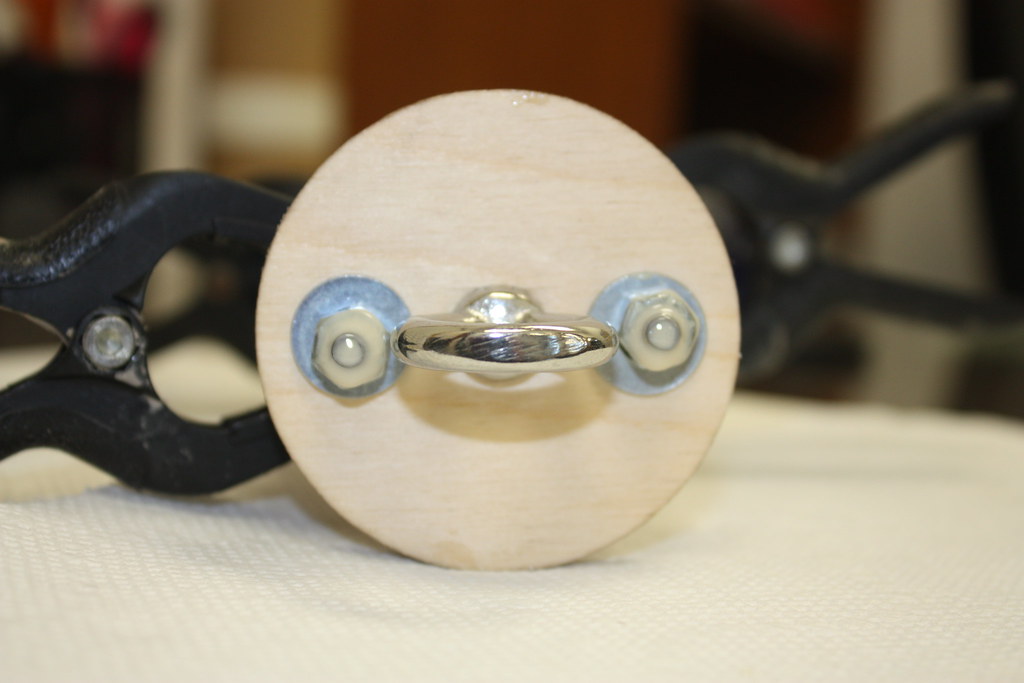
Next is the e-bay bulkheads.