A5tr0 An0n
Well-Known Member
- Joined
- Sep 29, 2012
- Messages
- 521
- Reaction score
- 10
Introduction:
In my recent attempt to start posting more, here is another build thread on a vehicle that has already been built well mostly built. It has not been painted or flown on the motor it was built for. Nonetheless the name of this vehicle is Progress. The reasoning for this is that when I started building it I had two thoughts (if you will) in mind. One was to "progress my MD building skills," and the other was well thats a secret that will be reviled in another one of my threads very shortly.
Okay enough blabbering, lets move onto the build.
Design:
Thoughts:
I knew I wanted to have a 54mm MD rocket and after playing around with OpenRocket I knew roughly what the design would be like. Basically I wanted to have hardly any space inside, to the point that recovery may not fit and I wanted to launch it on the L935 this I knew. I tend to build or in this case buy/modify rockets based on a motor I want to launch. I was getting ready to start buying all the parts and then viola! Madcow released their Tomach kit and it looked very similar to what I wanted, so to say the least I was interested. I played around with the kit in OpenRocket and that lead me to believe it would be fairly easy to modify it to meet my expectations. So the next thing I did was look at the price (which turned out to be the biggest motivating factor), it was priced I believe around $120 - $130 (introduction price) when I bought it. In comparison, to source the parts individually, just the airframe and nose cone would have cost me almost $100, so I jumped on the Tomach deal. So in conclusion, for a little bit more I got a little bit more. Now I have extra parts laying around, which IMO is never a bad thing.
Technical Specifications:
1. Nose Cone: ~6.1:1 Haack Series filament wound fiberglass with an Aluminum tip. The cone metrics are as follows: a base diameter of 2.205" (OD), a length of 13", a wall thickness of 0.079". The shoulder metrics are as follows: a diameter of 2.126", a length of 3.25", a wall thickness of 0.079". The installed shoulder extends past the nose cone at a length of 2.125", this is the amount of shoulder that will couple with the airframe. This results in a combined length of 15.125" and a total mass of 0.536lbs.
2. Airframe: Standard G12 filament wound fiberglass (natural). The airframe metrics are measured at 2.205" in diameter (OD), 36" in length but has since been cut down to 34.5" in length, 0.079" in wall thickness, and 1.25lbs in mass.
3. Fins: The fins used are the fins that come with the Tomach kit and thus is a three fin design. They are made from G10 fiberglass plate (natural) and the metrics of the unreinforced fins are measured as 7.63" root cord, ~2" tip cord, 2.366" span, 0.125" in thickness and a combined mass of 0.32lbs. However I have not left them unreinforced and did not leave them stock. For the modification I added a 0.25" bevel around the entire fin (leading/trailing edge and tip cord area). In regards to the reinforcement I added 2 layers of 3K 2x2 TW 270GSM (high density) aerospace grade carbon fiber in a tip-to-tip fashion (up to the edge of the bevel). The first layer stopped about ~1" from the edge of the fin where the second layer went up to the edge of the bevel (or 0.25" from the edge of the fin). I did this to allow for a thinner and smoother transition. With the tip-to-tip carbon fiber the metrics have slightly changed and and have resulted in measurements of 0.175" thickness (thickest place) and a mass of 0.41lbs.
4. Boattail: The boattail gives me greater aerodynamic properties, reduces stability and therefore ultimately gives me greater performance (altitude). So I chose to go with the CTI Pro54-TC, this also acts as a motor retainer/thrust plate and is flush with the airframe. It is made out of Aluminum 6061 and the metrics are measured at 2.2" in diameter (fore), 1.9" in diameter (aft), 1.42" in length, 0.16" in wall thickness, and a mass of 0.128lbs.
5. Motor Retention: Seeing as this is a minimum diameter bird their is no MMT inside. So that left me with 3 easy accessible options: friction fitting (uneasy about it), Aeropack minimum diameter retainer ( more than needed and less than ideal), and to make my own forward retainer (easy). I am not to keen on friction fitting the motor inside the airframe and seeing as this vehicle is also going to be used for another purpose this option is not possible. So that left me with two options. The Aeropack retainers are nice but they are big and bulky and take up too much needed space, so therefore I opted out of using one even though I had a left over 54mm MD retainer sitting on the table. So my last option was to design and machine one myself and that is the path I choose. More details to come later in the thread but it is basically a scaled up version of the one I built for ODIN.
6. Electronics/Recovery: The electronic/payload bay is located inside the nose cone, this being due to the fact that there is no room inside the airframe and why not use the empty space inside the nose cone? It just makes sense. The used flight computers/GPS systems/cameras are the TeleMega, Aim Xtra, GoPro 3 (black), and a 808 #20 (keychain camera). This gives me redundant tracking, redundant flight computers, a view of the flight (onboard) and a view of the recovery deployment/descent. Recovery is a 36" toroidal main parachute, yielding a Cd of 2.2 and thus should result in a descent rate of ~20ft/s. As a note, I normally like to bring them down fast but for the mass this parachute has a tight packing volume that is needed. There is no drogue parachute per se, the drogue is the deflated main that is tied together and released to fully inflate at 1500ft. The used harness is the 1500# 1/4" kevlar braided cord at 20ft in length. Since this is not a zipperless design the harness length should help prevent a zipper in addition to the material that is used.
7. Launch Approach: Naturally this will not be rod/rail launched. For the ODIN rocket I built a tower that is 6ft. long and adjustable to fit multiple rockets, therefore I will be using the same tower for this vehicle. I did some quick calculations and I estimated that if launch buttons were used it would take off ~1500ft from apogee. Not too drastic per se, but something about rail buttons on a minimum diameter rocket just does not add up. The maximum tower departure velocity is 111ft/sec.
Mostly designed in OpenRocket, however was cross checked in RASAero and RockSim.
3 dimensional representation of the internals.
It is what it is. Not 100% as built sim; that will come later. The dramatic CP/CG shift due to higher Mach flights starts to occur when the vehicle is around ~M1.625 and drops ~1 caliber in stability. This vehicles stability never drops below 1 caliber at any point in the flight. I feel that gives me enough insurance on stability.
Conclusion:
That about sums it up. If you have any questions or concerns then let me know. All the pictures/data will be posted shortly. Stay Tuned.
***Disclaimer:***
Here goes the usual disclaimer. Keep in mind when commenting that this is a build thread of a build that has already mostly happened and started almost a year ago. The construction techniques used may have been changed and/or modified since the time of this build. I am in no way telling you that these are the best or even right methods for constructing a rocket but rather the methods that I used at the time. Also this is a minimum diameter rocket but do not mistake that, for it being optimized.
Mat
In my recent attempt to start posting more, here is another build thread on a vehicle that has already been built well mostly built. It has not been painted or flown on the motor it was built for. Nonetheless the name of this vehicle is Progress. The reasoning for this is that when I started building it I had two thoughts (if you will) in mind. One was to "progress my MD building skills," and the other was well thats a secret that will be reviled in another one of my threads very shortly.
Design:
Thoughts:
I knew I wanted to have a 54mm MD rocket and after playing around with OpenRocket I knew roughly what the design would be like. Basically I wanted to have hardly any space inside, to the point that recovery may not fit and I wanted to launch it on the L935 this I knew. I tend to build or in this case buy/modify rockets based on a motor I want to launch. I was getting ready to start buying all the parts and then viola! Madcow released their Tomach kit and it looked very similar to what I wanted, so to say the least I was interested. I played around with the kit in OpenRocket and that lead me to believe it would be fairly easy to modify it to meet my expectations. So the next thing I did was look at the price (which turned out to be the biggest motivating factor), it was priced I believe around $120 - $130 (introduction price) when I bought it. In comparison, to source the parts individually, just the airframe and nose cone would have cost me almost $100, so I jumped on the Tomach deal. So in conclusion, for a little bit more I got a little bit more. Now I have extra parts laying around, which IMO is never a bad thing.
Technical Specifications:
1. Nose Cone: ~6.1:1 Haack Series filament wound fiberglass with an Aluminum tip. The cone metrics are as follows: a base diameter of 2.205" (OD), a length of 13", a wall thickness of 0.079". The shoulder metrics are as follows: a diameter of 2.126", a length of 3.25", a wall thickness of 0.079". The installed shoulder extends past the nose cone at a length of 2.125", this is the amount of shoulder that will couple with the airframe. This results in a combined length of 15.125" and a total mass of 0.536lbs.
2. Airframe: Standard G12 filament wound fiberglass (natural). The airframe metrics are measured at 2.205" in diameter (OD), 36" in length but has since been cut down to 34.5" in length, 0.079" in wall thickness, and 1.25lbs in mass.
3. Fins: The fins used are the fins that come with the Tomach kit and thus is a three fin design. They are made from G10 fiberglass plate (natural) and the metrics of the unreinforced fins are measured as 7.63" root cord, ~2" tip cord, 2.366" span, 0.125" in thickness and a combined mass of 0.32lbs. However I have not left them unreinforced and did not leave them stock. For the modification I added a 0.25" bevel around the entire fin (leading/trailing edge and tip cord area). In regards to the reinforcement I added 2 layers of 3K 2x2 TW 270GSM (high density) aerospace grade carbon fiber in a tip-to-tip fashion (up to the edge of the bevel). The first layer stopped about ~1" from the edge of the fin where the second layer went up to the edge of the bevel (or 0.25" from the edge of the fin). I did this to allow for a thinner and smoother transition. With the tip-to-tip carbon fiber the metrics have slightly changed and and have resulted in measurements of 0.175" thickness (thickest place) and a mass of 0.41lbs.
4. Boattail: The boattail gives me greater aerodynamic properties, reduces stability and therefore ultimately gives me greater performance (altitude). So I chose to go with the CTI Pro54-TC, this also acts as a motor retainer/thrust plate and is flush with the airframe. It is made out of Aluminum 6061 and the metrics are measured at 2.2" in diameter (fore), 1.9" in diameter (aft), 1.42" in length, 0.16" in wall thickness, and a mass of 0.128lbs.
5. Motor Retention: Seeing as this is a minimum diameter bird their is no MMT inside. So that left me with 3 easy accessible options: friction fitting (uneasy about it), Aeropack minimum diameter retainer ( more than needed and less than ideal), and to make my own forward retainer (easy). I am not to keen on friction fitting the motor inside the airframe and seeing as this vehicle is also going to be used for another purpose this option is not possible. So that left me with two options. The Aeropack retainers are nice but they are big and bulky and take up too much needed space, so therefore I opted out of using one even though I had a left over 54mm MD retainer sitting on the table. So my last option was to design and machine one myself and that is the path I choose. More details to come later in the thread but it is basically a scaled up version of the one I built for ODIN.
6. Electronics/Recovery: The electronic/payload bay is located inside the nose cone, this being due to the fact that there is no room inside the airframe and why not use the empty space inside the nose cone? It just makes sense. The used flight computers/GPS systems/cameras are the TeleMega, Aim Xtra, GoPro 3 (black), and a 808 #20 (keychain camera). This gives me redundant tracking, redundant flight computers, a view of the flight (onboard) and a view of the recovery deployment/descent. Recovery is a 36" toroidal main parachute, yielding a Cd of 2.2 and thus should result in a descent rate of ~20ft/s. As a note, I normally like to bring them down fast but for the mass this parachute has a tight packing volume that is needed. There is no drogue parachute per se, the drogue is the deflated main that is tied together and released to fully inflate at 1500ft. The used harness is the 1500# 1/4" kevlar braided cord at 20ft in length. Since this is not a zipperless design the harness length should help prevent a zipper in addition to the material that is used.
7. Launch Approach: Naturally this will not be rod/rail launched. For the ODIN rocket I built a tower that is 6ft. long and adjustable to fit multiple rockets, therefore I will be using the same tower for this vehicle. I did some quick calculations and I estimated that if launch buttons were used it would take off ~1500ft from apogee. Not too drastic per se, but something about rail buttons on a minimum diameter rocket just does not add up. The maximum tower departure velocity is 111ft/sec.
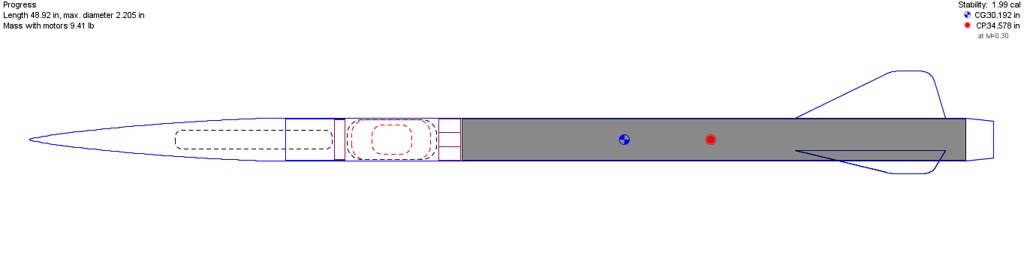
Mostly designed in OpenRocket, however was cross checked in RASAero and RockSim.
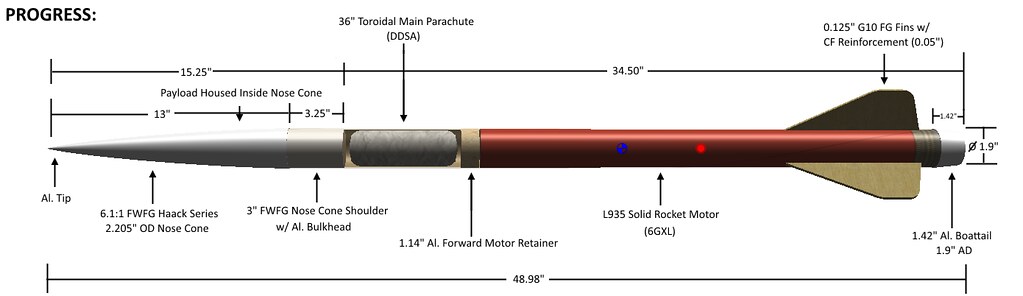
3 dimensional representation of the internals.
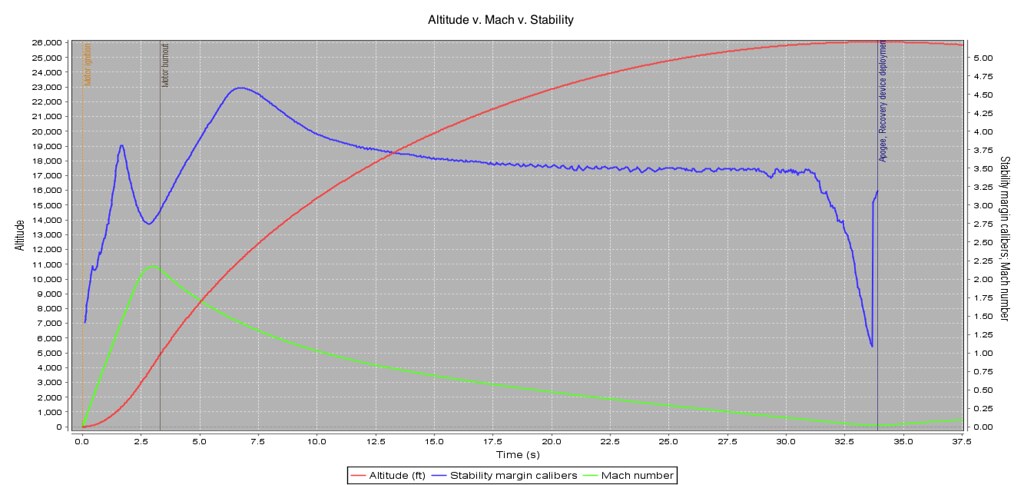
It is what it is. Not 100% as built sim; that will come later. The dramatic CP/CG shift due to higher Mach flights starts to occur when the vehicle is around ~M1.625 and drops ~1 caliber in stability. This vehicles stability never drops below 1 caliber at any point in the flight. I feel that gives me enough insurance on stability.
Conclusion:
That about sums it up. If you have any questions or concerns then let me know. All the pictures/data will be posted shortly. Stay Tuned.
***Disclaimer:***
Here goes the usual disclaimer. Keep in mind when commenting that this is a build thread of a build that has already mostly happened and started almost a year ago. The construction techniques used may have been changed and/or modified since the time of this build. I am in no way telling you that these are the best or even right methods for constructing a rocket but rather the methods that I used at the time. Also this is a minimum diameter rocket but do not mistake that, for it being optimized.
Mat
Last edited: