saustin
L2, NAR #86266
- Joined
- Jan 20, 2017
- Messages
- 71
- Reaction score
- 58
Hi TRF,
I'm a university student studying aerospace engineering. While we deal mostly with solids on this forum, I thought I'd share a project from the world of liquids.
Over the past year, I designed, built, and successfully hot-fired a liquid propellant rocket engine. The engine burns kerosene/liquid oxygen and was designed to produce 500 pounds of thrust at a chamber pressure of 600 psi.
I fired the engine at the Friends of Amateur Rocketry (FAR) site out in California in August. Ignition was achieved on the first attempt, and the engine burned successfully for 2.55 seconds. Among the many people who made this project possible are Rick Mascheck of FAR and Dave Crisalli of the Reaction Research Society.
Video of the test is here:
Best,
Sam
I'm a university student studying aerospace engineering. While we deal mostly with solids on this forum, I thought I'd share a project from the world of liquids.
Over the past year, I designed, built, and successfully hot-fired a liquid propellant rocket engine. The engine burns kerosene/liquid oxygen and was designed to produce 500 pounds of thrust at a chamber pressure of 600 psi.
I fired the engine at the Friends of Amateur Rocketry (FAR) site out in California in August. Ignition was achieved on the first attempt, and the engine burned successfully for 2.55 seconds. Among the many people who made this project possible are Rick Mascheck of FAR and Dave Crisalli of the Reaction Research Society.
Video of the test is here:
Best,
Sam
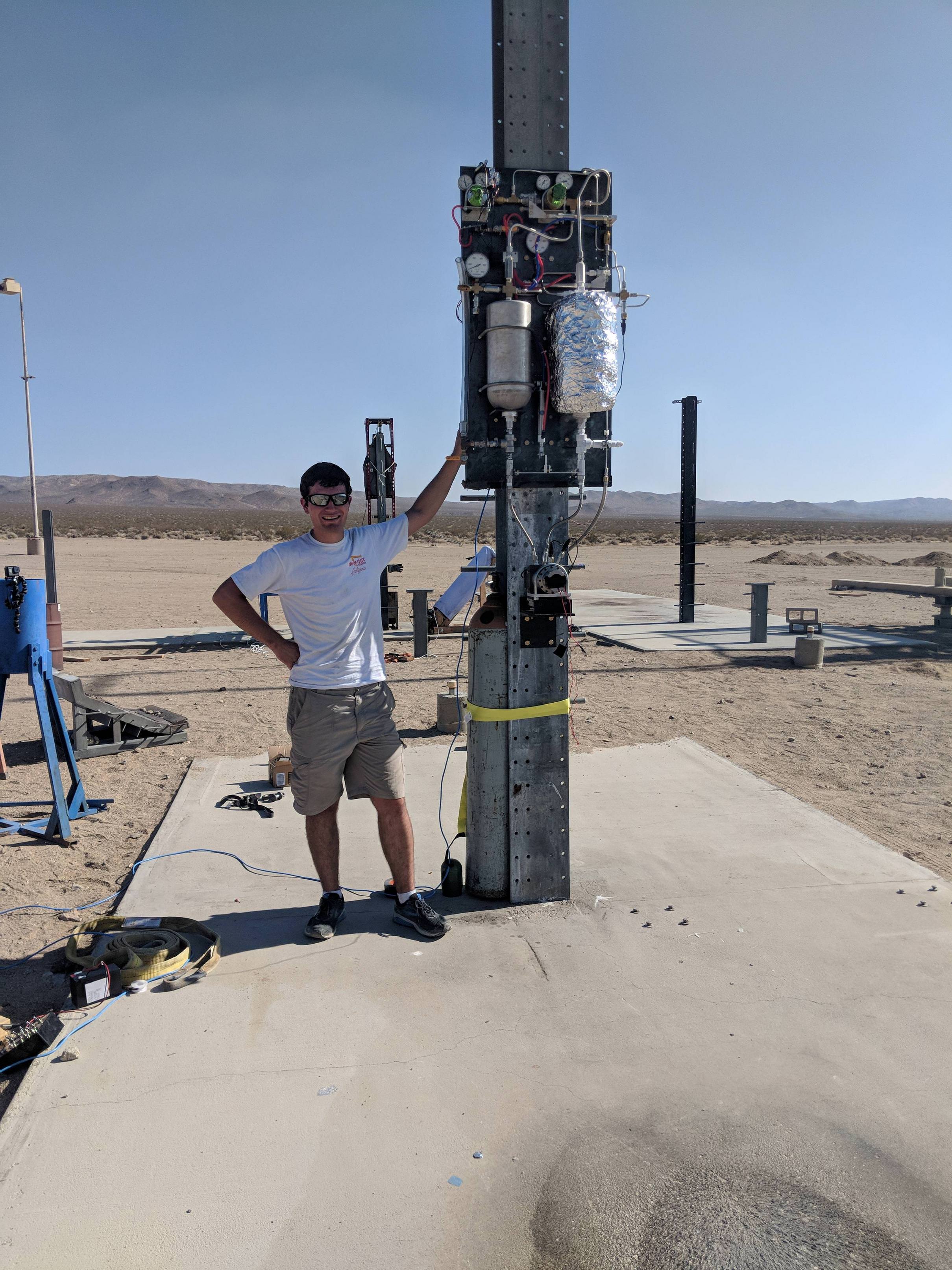
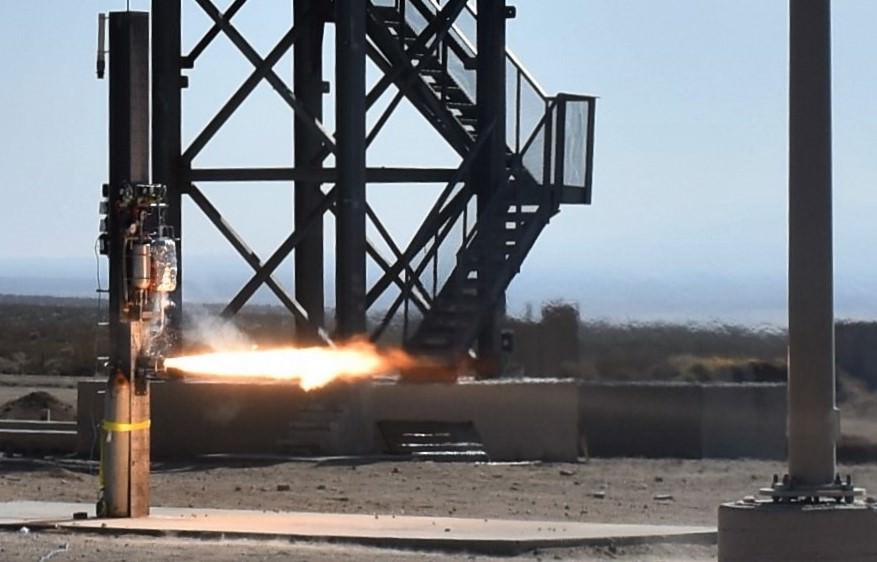
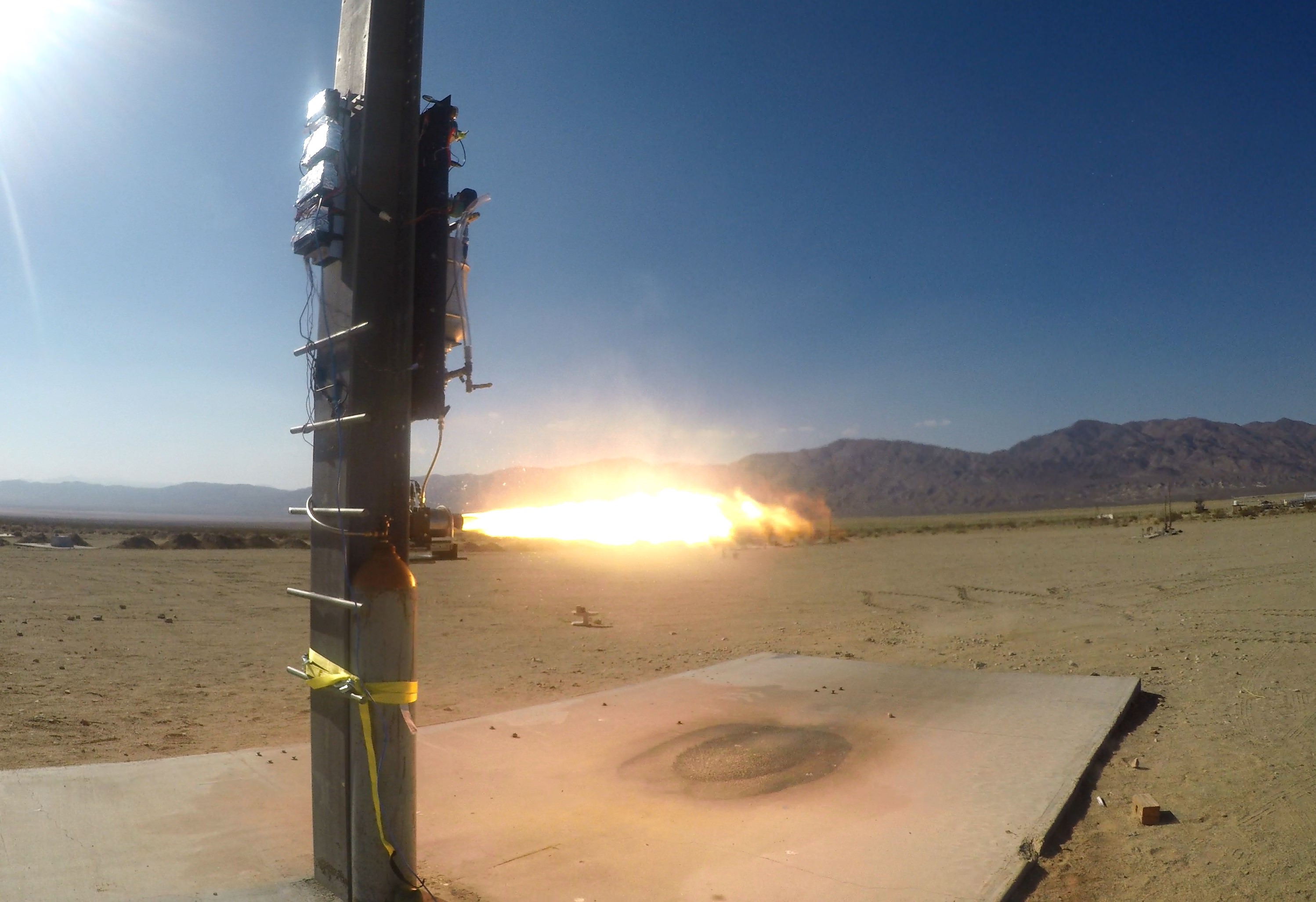