smapdiage9
Well-Known Member
- Joined
- Mar 14, 2009
- Messages
- 442
- Reaction score
- 3
I purchased the Extreme Wildman 4" kit a few months ago for a couple of reasons. First, it was the next kit in the Wildman line that I didn't own yet, and second because I wanted something a bit nicer and roomier for L2 flights than my GLR Vertical Assault. The VA has been my workhorse for several years, and I certed both L1 and L2 with it, so it's time to burn propellant with a rocket that's a little bit bigger and slicker. The long term goals for this include working my way toward an ultimate wildman build (basically the same rocket 50% bigger) which I've wanted to do forever, and finally having a payload big enough to carry a decent camera.
This is also the first rocket project I've undertaken that really has to be flown on at least a J; I guess technically an I800 will get it off the rail at a decent speed, but apogee at 600 feet seems kind of anticlimactic. By the stock rkt file a K535 will get it to 4.4k and an L935 to under 10k. I'm not much of a sport rocket guy as high performance stuff has always caught my attention better, but the realities of my local waiver mean I might as well have some loud fun flights below 10k so here we go.
The kit has been built better by other people so I won't document that exactly. What I will say is that this was the first HPR build where I broke stuff down into work types instead of build segments, meaning that I used a silver sharpie to replicate the markings done in the kit instructions for measurements on each aspect of the airframe. Then I did all of the drilling operations which could be accomplished up front, and following that I completed all of the sanding that could be done up front. These two decisions made the actual gluing and assembly a total breeze.
Fin alignment was the first major effort. I used a level and a square to clamp my body tube between two pieces of angle iron with the fin slot exactly at the top, then taped the level to the fin to make it sit upright.
All three fins tacked in place with rocketpoxy, they are set but not fully cured:
The directions were written for a slightly thinner base epoxy (west) with translucent green FG tubing that is no longer supplied. Using rocket poxy, chopped carbon fiber, and the black tubing the injections went well but I had no way to verify how far along the fin root they would cover. Additionally, I found that tilting the airframe did little to flow the epoxy as even when thinned with a lot of black pigment the viscosity with the fibers in it was quite high. To give myself peace of mind I did initial injections with 10ml per side in the stock hole locations (1/3 and 2/3 down the root) and allowed them to set up. Then, I drilled inspection holes nearer the two ends of the fin root and found that it really hadn't flown that far, so I made a second injection with much thinner aeropoxy near the forward and aft end of each fin through those inspection holes to assist with reaching the centering rings and rest of the root. Ultimately each fin received its 25ml of rocketpoxy distributed across four holes per side instead of two with the fin-cr joints getting some additional aeropoxy for good measure (mainly because I was out of rocketpoxy for a couple weeks).
When doing external fillets I also found that the stock 1/4" injection hole locations were not fully covered by the fillet radius I wanted to use which was kind of annoying. On the next one I'll probably intentionally size my injection holes to the size of my syringes (smaller than 1/4) and make sure that my holes are a little closer to the fin.
My realization that this is going to be a big damn rocket occurs as I realize I can't actually assemble it indoors with my low ceilings:
I used the Aeropack instructions to determine my motor tube overhang for the retainer. Hopefully it works out because I still haven't tested it with any 75mm hardware.
I am the world's worst builder in terms of finishing aesthetics, and it probably doesn't help that I really don't care about good paint jobs anymore. This is the biggest rocket I've ever built, and the tremendous quantity of epoxy required for fillets meant bubbles and sunken portions were even worse than normal. Yes I spread the rocketpoxy out thin to get some bubbles out, but it just never seems to settle perfectly for me on big ass fins like this. My reently purchased harbor freight oscillating sander was used judiciously to even things out. Again, I hate painting. Because of that I decided to commission a wrap from StickerShock23. Knowing that the wrap would cover everything but the tip of the nosecone, the fins, and the tailcone, I was only required to paint the fins on this rocket. Black gloss got rid of the gray streaks from sanding and beveling, but also made the fillets look even worse. No worry, those will be covered up soon.
I wanted something a bit outrageous and trippy for this build, so I chose a pink fractal pattern for the entire airframe. I started the wrap on the nosecone, which would turn out surprisingly to be the easiest part. The large tubes were challenging, and if I do it again I'm definitely gonna use saw horses to set up a little rotisserie instead of just doing it on a table.
Nosecone and payload in progress:
The whole rocket wrapped:
This thing exactly fits my aesthetic demands: it's lazily constructed up close, but from 10 feet away looks amazing. The seams, bubbles, and other little errors totally disappear once you step back and I'm extremely happy with the way it turned out.
This week my goal is to figure out the avionics bay and do some ground tests. I've always been a friction fit guy and never used shear pins, which this one definitely uses, so it'll be interesting to see how that goes. I've got an 84" pink parachute as the main to match the theme. I also drilled a mounting hole in the booster tube to positively fix my keychain camera, which I've traditionally just held on with gaffer tape on other L2 flights.
This is also the first rocket project I've undertaken that really has to be flown on at least a J; I guess technically an I800 will get it off the rail at a decent speed, but apogee at 600 feet seems kind of anticlimactic. By the stock rkt file a K535 will get it to 4.4k and an L935 to under 10k. I'm not much of a sport rocket guy as high performance stuff has always caught my attention better, but the realities of my local waiver mean I might as well have some loud fun flights below 10k so here we go.
The kit has been built better by other people so I won't document that exactly. What I will say is that this was the first HPR build where I broke stuff down into work types instead of build segments, meaning that I used a silver sharpie to replicate the markings done in the kit instructions for measurements on each aspect of the airframe. Then I did all of the drilling operations which could be accomplished up front, and following that I completed all of the sanding that could be done up front. These two decisions made the actual gluing and assembly a total breeze.
Fin alignment was the first major effort. I used a level and a square to clamp my body tube between two pieces of angle iron with the fin slot exactly at the top, then taped the level to the fin to make it sit upright.
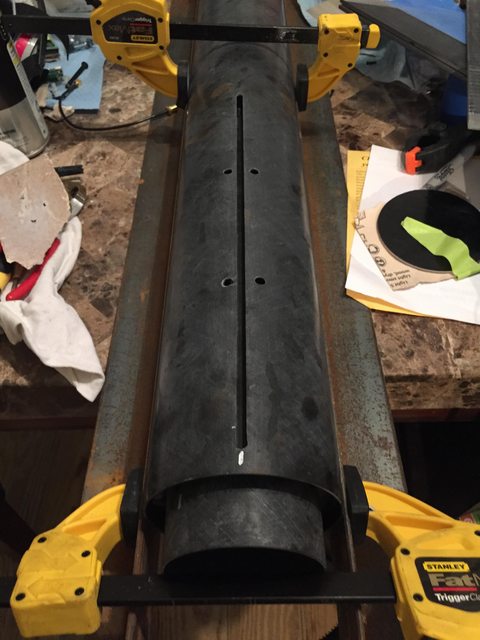

All three fins tacked in place with rocketpoxy, they are set but not fully cured:
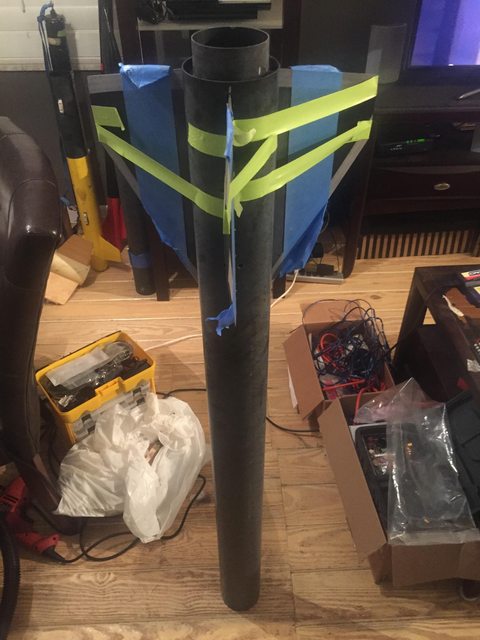
The directions were written for a slightly thinner base epoxy (west) with translucent green FG tubing that is no longer supplied. Using rocket poxy, chopped carbon fiber, and the black tubing the injections went well but I had no way to verify how far along the fin root they would cover. Additionally, I found that tilting the airframe did little to flow the epoxy as even when thinned with a lot of black pigment the viscosity with the fibers in it was quite high. To give myself peace of mind I did initial injections with 10ml per side in the stock hole locations (1/3 and 2/3 down the root) and allowed them to set up. Then, I drilled inspection holes nearer the two ends of the fin root and found that it really hadn't flown that far, so I made a second injection with much thinner aeropoxy near the forward and aft end of each fin through those inspection holes to assist with reaching the centering rings and rest of the root. Ultimately each fin received its 25ml of rocketpoxy distributed across four holes per side instead of two with the fin-cr joints getting some additional aeropoxy for good measure (mainly because I was out of rocketpoxy for a couple weeks).
When doing external fillets I also found that the stock 1/4" injection hole locations were not fully covered by the fillet radius I wanted to use which was kind of annoying. On the next one I'll probably intentionally size my injection holes to the size of my syringes (smaller than 1/4) and make sure that my holes are a little closer to the fin.
My realization that this is going to be a big damn rocket occurs as I realize I can't actually assemble it indoors with my low ceilings:
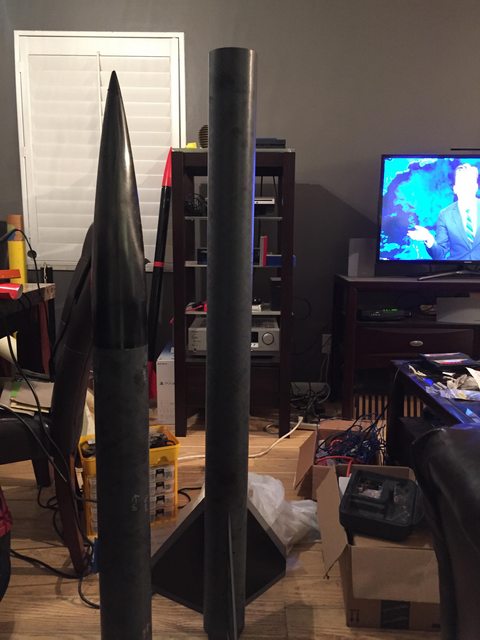
I used the Aeropack instructions to determine my motor tube overhang for the retainer. Hopefully it works out because I still haven't tested it with any 75mm hardware.
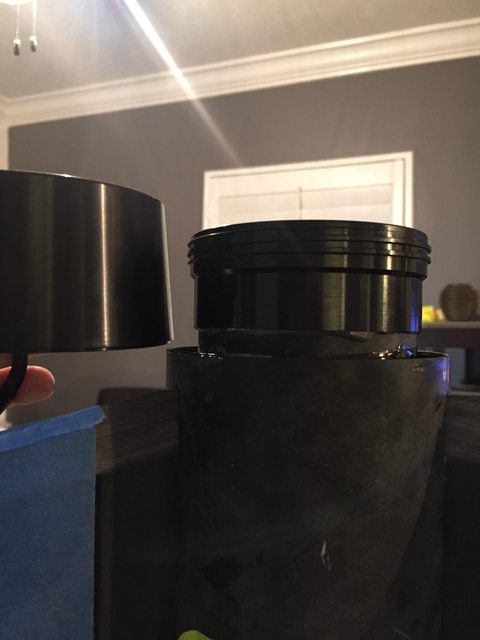
I am the world's worst builder in terms of finishing aesthetics, and it probably doesn't help that I really don't care about good paint jobs anymore. This is the biggest rocket I've ever built, and the tremendous quantity of epoxy required for fillets meant bubbles and sunken portions were even worse than normal. Yes I spread the rocketpoxy out thin to get some bubbles out, but it just never seems to settle perfectly for me on big ass fins like this. My reently purchased harbor freight oscillating sander was used judiciously to even things out. Again, I hate painting. Because of that I decided to commission a wrap from StickerShock23. Knowing that the wrap would cover everything but the tip of the nosecone, the fins, and the tailcone, I was only required to paint the fins on this rocket. Black gloss got rid of the gray streaks from sanding and beveling, but also made the fillets look even worse. No worry, those will be covered up soon.
I wanted something a bit outrageous and trippy for this build, so I chose a pink fractal pattern for the entire airframe. I started the wrap on the nosecone, which would turn out surprisingly to be the easiest part. The large tubes were challenging, and if I do it again I'm definitely gonna use saw horses to set up a little rotisserie instead of just doing it on a table.
Nosecone and payload in progress:
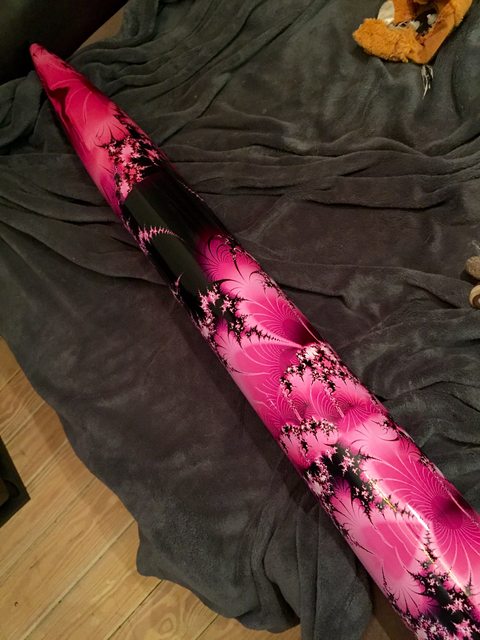
The whole rocket wrapped:
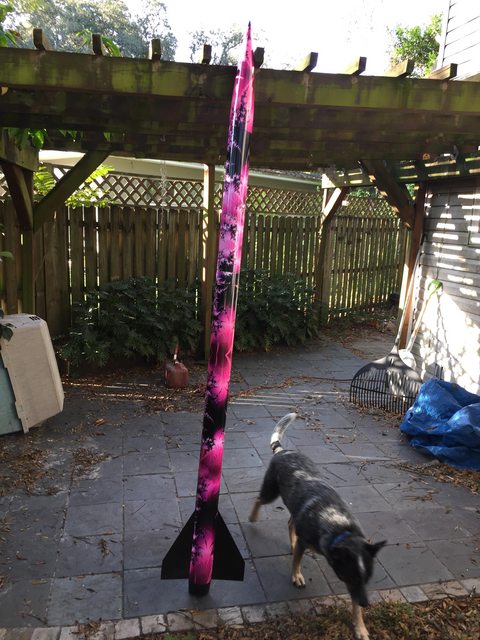
This thing exactly fits my aesthetic demands: it's lazily constructed up close, but from 10 feet away looks amazing. The seams, bubbles, and other little errors totally disappear once you step back and I'm extremely happy with the way it turned out.
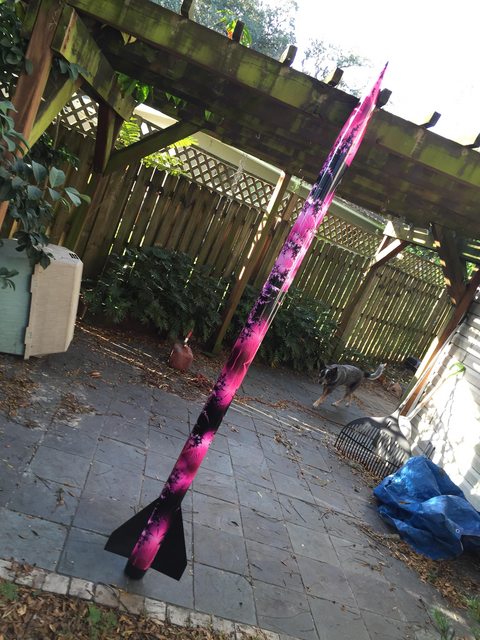
This week my goal is to figure out the avionics bay and do some ground tests. I've always been a friction fit guy and never used shear pins, which this one definitely uses, so it'll be interesting to see how that goes. I've got an 84" pink parachute as the main to match the theme. I also drilled a mounting hole in the booster tube to positively fix my keychain camera, which I've traditionally just held on with gaffer tape on other L2 flights.
Last edited: