- Joined
- Mar 27, 2013
- Messages
- 22,537
- Reaction score
- 14,953
The sustainer's motor mount is based on some pretty standard mounts, except that it lacks a rear centering ring.
Thanks to Eric, I've got a centering ring that I needed to get the build moving forward. Now, I'm not putting in a rear centering ring because I need to create those "tunnels" for whatever recovery device I finally decide on using for the booster. The fins will mount to the motor mount, and internal fillets will hold the mount securely.
I finally opted not to add a payload section to the build. In my experience handling my zipperless design Yellow Jacket upscale, I keep having the fin can fall to the ground (usually pebbly concrete, or some other hard abrasive, fin-chewing, surface (gravel)). The problem with the Yellow Jacket is that the separation joint is below 1/3 the length of the rocket, my natural grabbing point. The Velociraptor has the large green section and the decal (VELOCIRAPTOR) that I don't want to cut, which puts the separation joint closer to 1/2 the rocket's length. To me, that's a guarantee that the fin can will fall (repeatedly) to the ground and get damaged, and I don't want that to happen to my rocket.
Since the body tube is longer than 18", I decided not cut down two complete body tubes to make up the length needed. So, I've decided to make the shorter section the fin can. I've marked it up, and slotted the tube for a couple of the fins (I could have done all of them, but I wanted to take a WIP photo).
BTW... I like to align my launch lugs with my engine hook (hence the clear markings I make for it). That way the engine hook is out of the way when I connect the clips to the igniter.
After getting the new fins cut out, the hard parts begin... Making those Talon fins, and all of the boat tail work.
However, I'm working on 2 hours of sleep right now. So, I'll get on it when I'm fresh.
TBC
Jim
.
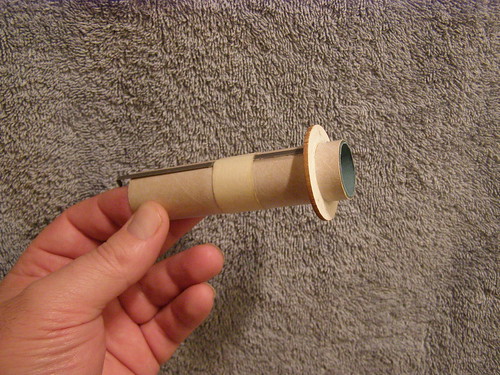

Thanks to Eric, I've got a centering ring that I needed to get the build moving forward. Now, I'm not putting in a rear centering ring because I need to create those "tunnels" for whatever recovery device I finally decide on using for the booster. The fins will mount to the motor mount, and internal fillets will hold the mount securely.
I finally opted not to add a payload section to the build. In my experience handling my zipperless design Yellow Jacket upscale, I keep having the fin can fall to the ground (usually pebbly concrete, or some other hard abrasive, fin-chewing, surface (gravel)). The problem with the Yellow Jacket is that the separation joint is below 1/3 the length of the rocket, my natural grabbing point. The Velociraptor has the large green section and the decal (VELOCIRAPTOR) that I don't want to cut, which puts the separation joint closer to 1/2 the rocket's length. To me, that's a guarantee that the fin can will fall (repeatedly) to the ground and get damaged, and I don't want that to happen to my rocket.
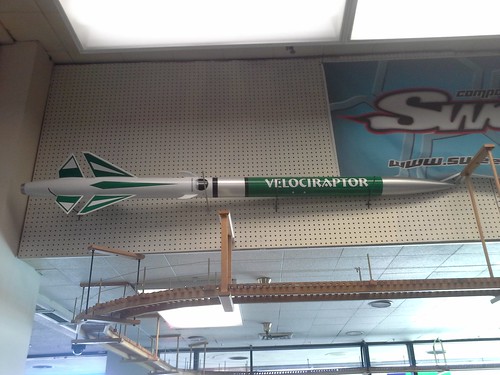
Since the body tube is longer than 18", I decided not cut down two complete body tubes to make up the length needed. So, I've decided to make the shorter section the fin can. I've marked it up, and slotted the tube for a couple of the fins (I could have done all of them, but I wanted to take a WIP photo).
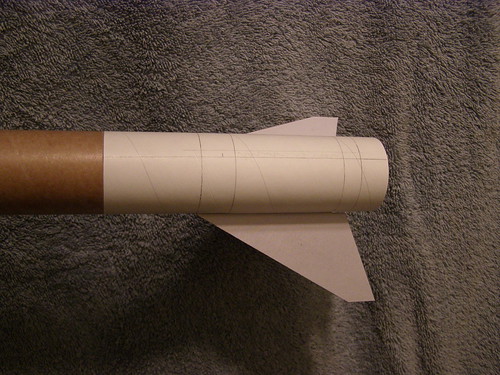
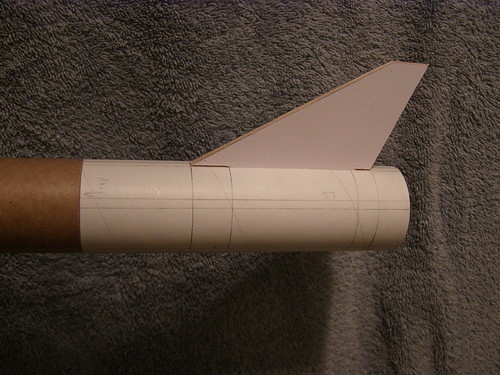
BTW... I like to align my launch lugs with my engine hook (hence the clear markings I make for it). That way the engine hook is out of the way when I connect the clips to the igniter.
After getting the new fins cut out, the hard parts begin... Making those Talon fins, and all of the boat tail work.
However, I'm working on 2 hours of sleep right now. So, I'll get on it when I'm fresh.
TBC
Jim
.
Last edited: