Note Here - I am typing this for flyers who are interested in and or are curious about flying hybrid rocket motors. I hope to give the reader a basic understanding of what is needed / involved in order to fly basic Urbanski-Colburn valved hybrids (a.k.a. U/C valve). A search of John Urbanski & Bill Colburn will net more info for the reader regarding the floating valve (U/C valve) system. For this thread I will be referring strictly to the Ground Support Equipment, and not the motors themselves.
Since 2009, the hybrid revolution has seen a steady decline in interested users. Clubs everywhere no longer use or have sold off their own ground support equipment, also called GSE, making it tough for die-hard flyers to fly hybrid rocket motors. Of course, if you are a die-hard hybrid flyer, you probably own your GSE anyway. As of this typing, this is the hybrid ground support that I have been bringing together from a couple different sources. Also, as of this typing, I am only about 85% finished with everything I will need to be self sufficient as a hybrid flyer, no matter the launch venue.
Starting with the oldest piece of ground support I own, is my variation of the ProRail base, made famous by John Coker...
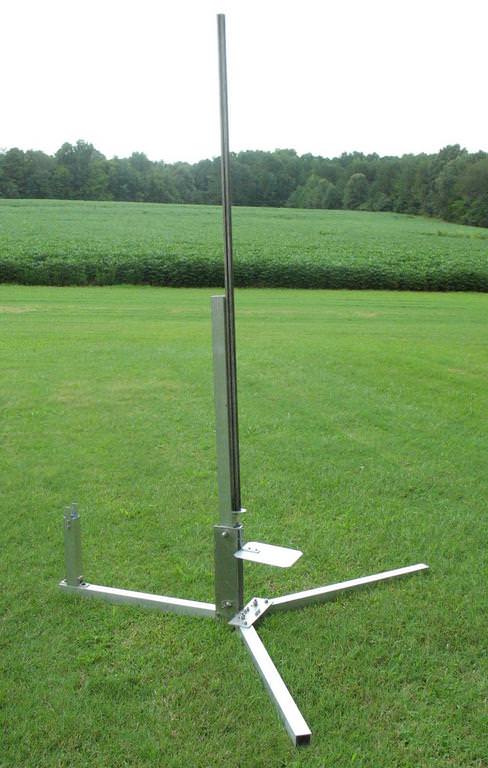
Any launch pad will work, but dedicating a pad strictly for hybrids is a must, due to the amount of support that will be needed on sight. Like everyone here on this forum, I like to build most everything I will use, and I am rather proud of my launch pad. Because of the amount of equipment you will be "humping" out into the field, lightweight is key.
I have owned this pad for a while now, so I felt it needed a little upgrading. I originally assembled the pad with zinc coated hardware, and as you can see, it has become a little corroded. The threads were beginning to seize, so I took this mess...
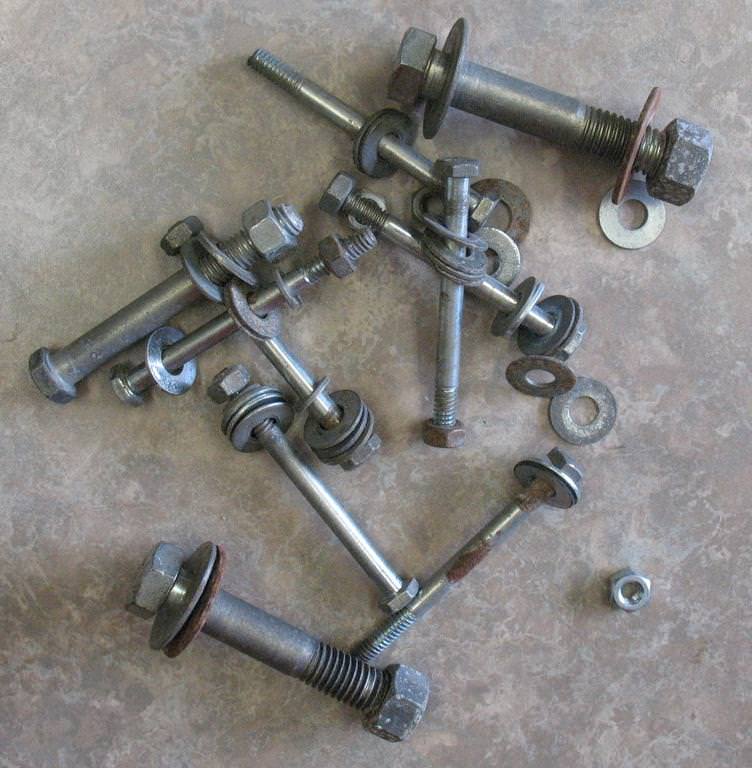
And replaced it with stainless steel from (s)Lowes Rocket Improvement...
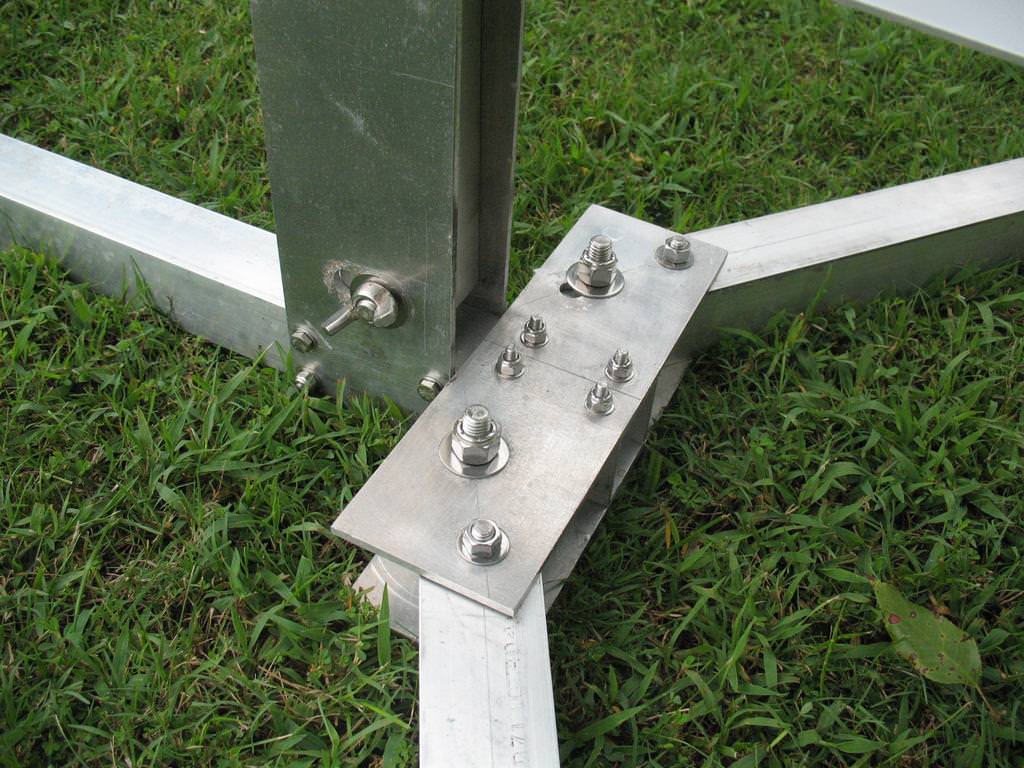
This season has also ushered in a blast deflector, as even hybrids can cause ground fires...
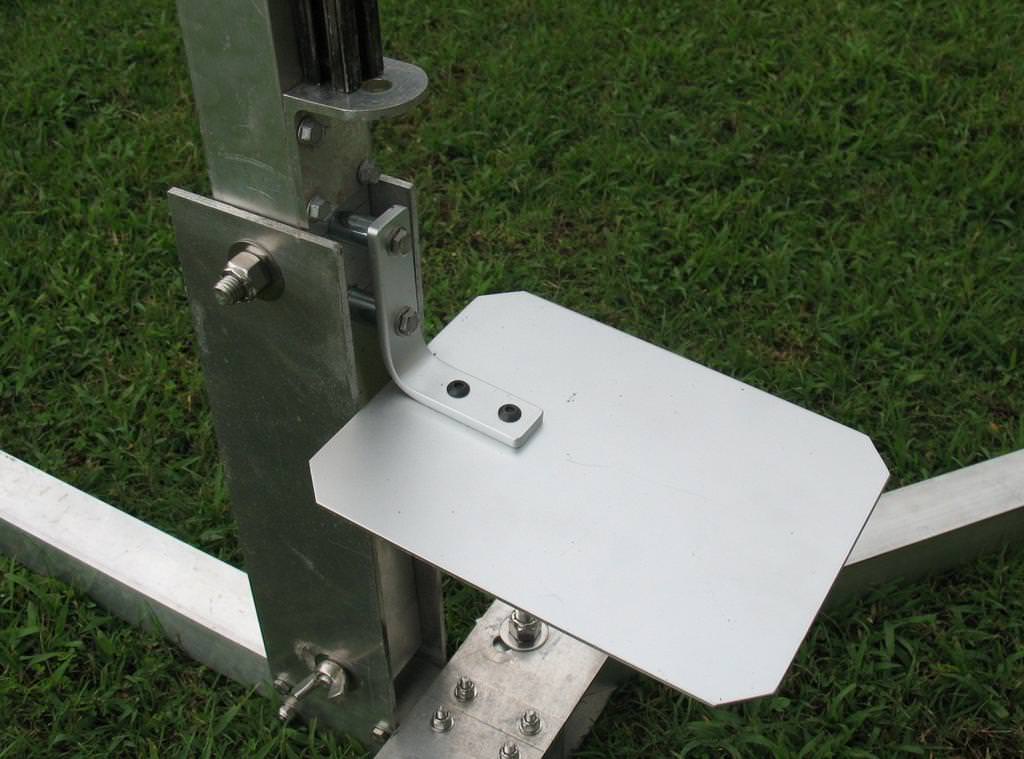
The deflector is away from, and is far away enough from the base of the rocket so not to scorch the end of the air frame.
Next we focus on the heart of the hybrid ground support, the central junction box.
Last edited: